12 Common Challenges in Manufacturing Solutions and How to Overcome Them
- vanayarama
- Mar 18
- 4 min read
Manufacturing solutions are the backbone of any production process, playing a crucial role in ensuring efficiency and quality. However, manufacturers often face various challenges that can impede progress. This blog explores common hurdles in the manufacturing industry and offers practical solutions to overcome them, making the journey smoother and more productive.
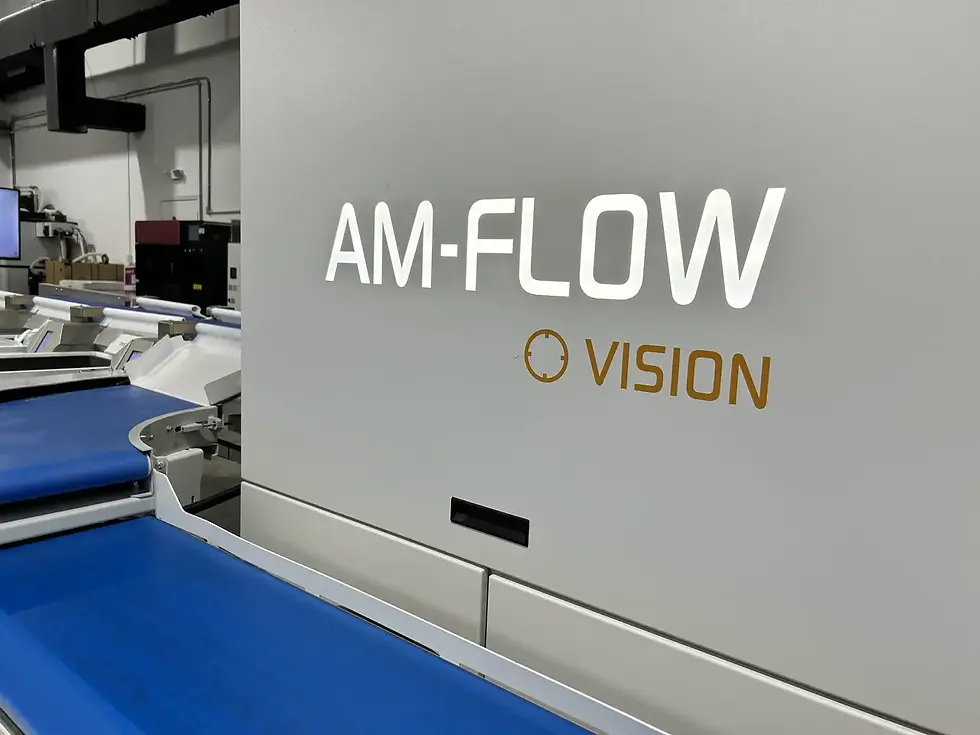
1. Ensuring Quality Control
Maintaining consistent quality can be a challenging task. Implementing a robust quality control system helps in detecting defects early and ensuring that products meet the required standards. Advanced techniques, such as real-time monitoring, allow for immediate adjustments during production, reducing waste and increasing efficiency.
Enhancing quality control involves leveraging technology like IoT and AI, which provide insights into the production process. This technology-driven approach not only catches deviations from the norm but also anticipates potential flaws, ensuring the final product's integrity. Furthermore, statistical process control can reveal subtle shifts in production, leading to proactive rather than reactive problem-solving.
2. Optimizing Production Efficiency
Inefficient production processes can lead to delays and increased costs. Streamlining operations and adopting lean manufacturing techniques can significantly enhance efficiency. For instance, applying Just-In-Time (JIT) methods can reduce inventory costs and waste, allowing manufacturers to meet customer demands quickly and effectively. This results in streamlined processes and fine-tuned production cycles.
Implementing automated systems tailored to specific operational needs can propel efficiencies forward. These systems ensure consistent output by minimizing human error and improving accuracy. Real-time data tracking empowers operators to identify production bottlenecks swiftly, allowing enterprises to allocate resources optimally and maintain momentum through shifting market demands.
3. Managing Supply Chain Disruptions
Supply chain disruptions can halt production lines. Developing a robust supply chain strategy with multiple suppliers can reduce the impact of these interruptions. Incorporating digital solutions, like Cloud-based inventory systems, offers real-time insights into stock levels, supplier reliability, and logistics flows, ensuring seamless operations even in turbulent times.
Resilient supply chains often leverage Industry 4.0 solutions to automate complex networks. Technology such as predictive analytics and AI-driven forecasting minimizes risk by identifying potential disruptions before they affect the production line. Such foresight enables manufacturers to adjust their strategies proactively, ensuring consistency in output and fulfilment.
4. Dealing with Skilled Labor Shortages
A shortage of skilled labor can affect production quality. Investing in employee training and exploring automation solutions can mitigate this challenge. By fostering partnerships with educational institutions, businesses can attract fresh talent and implement targeted upskilling programs, equipping the current workforce to handle emerging technologies and processes.
Embracing automation not only compensates for labor gaps but encourages existing employees to focus on value-added tasks. Solutions such as robotic process automation replace redundant activities, while effective change management involves the workforce in the digital transformation. This approach minimizes resistance by highlighting career development opportunities within the evolving manufacturing landscape.
5. Integrating Advanced Technologies
Adopting new technologies can be daunting. Focusing on incremental integration and ensuring staff are adequately trained can ease this transition. Start by evaluating processes that can benefit most from automation and leverage solutions like 3D printing. This revolutionary method reduces lead times and material costs, presenting myriad possibilities for product design and customization.
Using IoT and real-time analytics transforms operations by enabling seamless communication between interconnected devices. Such connectivity optimizes workflows, facilitating data-driven decision-making that enhances productivity. Fostering a culture of continuous innovation empowers teams to seek incremental improvements, build expertise, and adapt swiftly to evolving technological landscapes.
6. Controlling Production Costs
Escalating production costs can eat into profits. Implementing cost-control measures and continuous process analysis can help manage expenses. Solutions such as lean manufacturing principles refine resource allocation and minimize waste, while comprehensive cost analysis identifies inefficiencies and variances, ensuring budget adherence and financial stability.
7. Maintaining Equipment Effectiveness
Regular equipment breakdowns can cause costly downtimes. Establishing a preventive maintenance schedule can greatly enhance equipment longevity. Through predictive maintenance powered by IoT and smart sensors, manufacturers can anticipate and rectify issues early, reducing repair costs and ensuring consistent operational readiness without unforeseen disruptions.
8. Enhancing Product Innovation
Staying innovative can be challenging in a competitive market. Encouraging a culture of creativity and regular market analysis can fuel product advancements. Engage employees with brainstorming sessions and deploy rapid prototyping tools that aid in testing concepts quickly, allowing for agile responses to shifting customer needs and emerging industry trends, ensuring sustained market leadership.
9. Ensuring Compliance with Regulations
Navigating complex regulatory environments can be intricate. Staying updated on regulations and implementing compliance management systems will ensure smooth operations. Regular audits and risk assessments bridge knowledge gaps, while creating a robust compliance culture safeguards against costly penalties, fostering trust between regulators and industry stakeholders.
10. Ensuring Workplace Safety
Safety hazards can threaten both employees and productivity. Instituting comprehensive safety protocols and ongoing training programs can create a safer workplace. Implementing automated safety systems, such as machine sensors and ergonomic designs, further enhances security, protecting employees and mitigating interruptions from potential hazards.
11. Adapting to Market Changes
Market dynamics can shift rapidly, impacting demand. Being flexible and responsive, with a strong market feedback loop, can help adapt to these variations. Regularly engaging with customers and leveraging predictive analytics can inform product development, shorten time-to-market, and maintain alignment with consumer preferences, ensuring long-term competitiveness and resilience.
12. Improving Customer Satisfaction
High customer satisfaction is crucial for success. Engaging with customers and adapting to their needs can strengthen relationships and boost business growth. Implementing a robust customer relationship management (CRM) system facilitates personalized interactions, feedback collection, and service enhancement, which translate into loyal clientele and positive brand reputation.